What Is Activity-Based Costing: Full Guide With Systems, Formulas & Examples for 2025
Are you confused by activity-based costing (ABC) methods? Do you wish you knew how to implement an ABC system so that you can cut production costs, decrease waste and increase profits? You should read our guide, which will open your eyes to the world of activity-based costing.
Key Takeaways: Activity-Based Costing 101
- An activity-based costing system can help companies accurately price products, improve manufacturing efficiency and eliminate waste by breaking down production resources and their associated costs.
- An activity-based costing system is best for large organizations that produce multiple products due to the complex nature of the method.
- Smaller companies that produce just one or two products or that don’t work on complex tasks should stick with traditional costing systems.
One of the hardest things for manufacturing organizations is coming up with pricing that keeps their products competitive and profitable. The problem is that traditional costing methods can generate waste and keep companies from earning the profits they desire. This is where activity-based costing systems come into play.
In this guide, we’ll take a look at activity-based costing. We’ll explain what it is, how it works and the pros and cons of the system. We will even show you an example of the math that’s involved (don’t worry, it’s not complicated). If you want to implement an ABC system but don’t know where to start, you’re in the right place.
What Is Activity-Based Costing
Activity-based costing is a method used to allocate overhead production costs. The ABC system breaks down manufacturing overhead into cost pools such as machines, raw materials, salaries, utilities and anything else that costs money. Each cost pool is then filled with individual cost objects (items) like electric, water, gas and all the rest that goes into making a product.
With an activity-based costing system, manufacturers can see how efficient their production system is, where overspending occurs and where waste is present. If you think this sounds similar to the Lean project management methodology, you’re right. In fact, management accounting is a key part of the Six Sigma methodology.
Avoid Costly Project Management Mistakes – Get Free Tips Today!
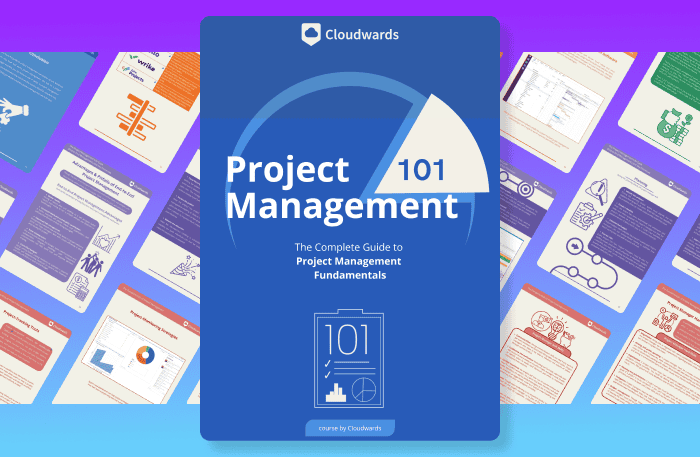
- Discover 10 fundamentals of project management
- Understand step-by-step plans for PM execution
- Learn tips to avoid 5 common mistakes by beginners
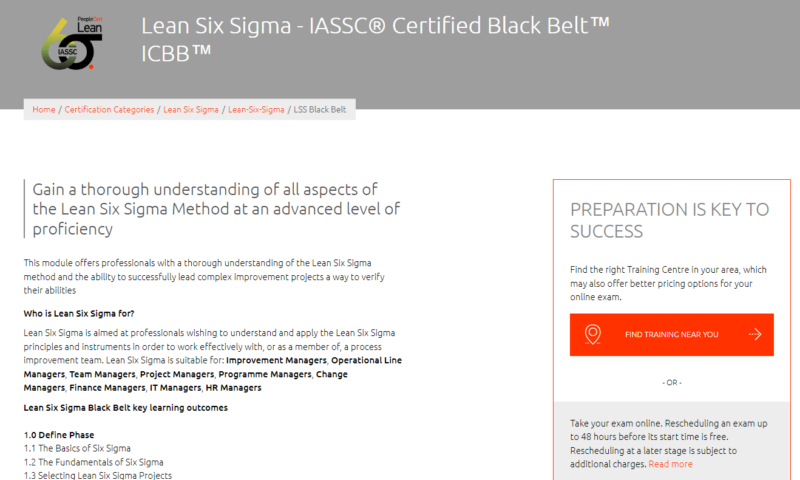
can benefit from a PeopleCert certification in Lean Six Sigma.
Traditional Costing vs Activity-Based Costing
Traditional and activity-based costing systems are similar in that they’re both used to assign overhead costs to products. However, they couldn’t be more different in practice. A traditional costing method assigns costs to products via one cost driver, such as labor. As you can imagine, using just one cost driver can lead to inaccurate cost measurements.
Activity-based costing calculates overhead (indirect expenses) costs by taking multiple cost drivers (machine setup costs, labor, inspections, utilities, etc.) into account before assigning product costs. Activity-based costing is an incredibly precise method used by large companies needing accurate figures when allocating overhead costs.
How Activity-Based Costing (ABC) Works
Now that we have covered what activity-based costing is, let’s take a closer look at how it works. Below, we’ll cover the steps you need to take to implement a cost accounting ABC system.
Identify Activities
The first step in an activity-based costing system is to identify activities (cost drivers) that cost you money to make your product. It’s here that you need to take items like utilities, inspections, direct labor costs, research and development, machine costs and purchasing into account. Once you have determined your activities, you can start breaking them down into cost pools.
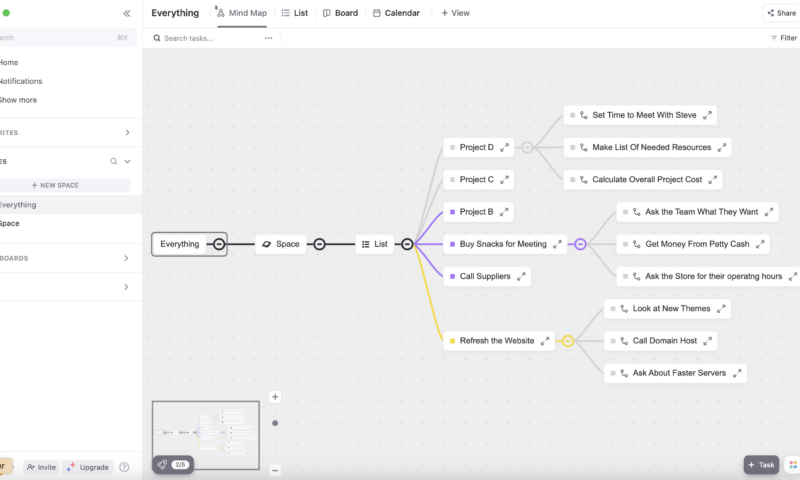
visualize activities and what their cost pools may look like.
Create Cost Pools
Now that you have determined your cost drivers (items that cost you money), you can break them down into cost pools (groups of resources). For example, we can take the utility cost driver and break it down into a cost pool that contains electric, gas, water and waste disposal bills. By doing this, you can see precisely what in each activity will hit your bottom line.
Calculate Costs
The next step is to assign costs to each resource in each cost pool. You do this by giving a unit of measurement to each item. For example, you can use dollars for purchases or hours for each machine used to produce the product. Alternatively, you could use labor costs for each machine used. Go through each item in each pool and assign a unit that can be easily measured.
Do the Math
Now it’s time for the fun part: math. During this part of the process, you will look at the variable and fixed costs you gave each resource in your cost pools and determine the cost driver rate.
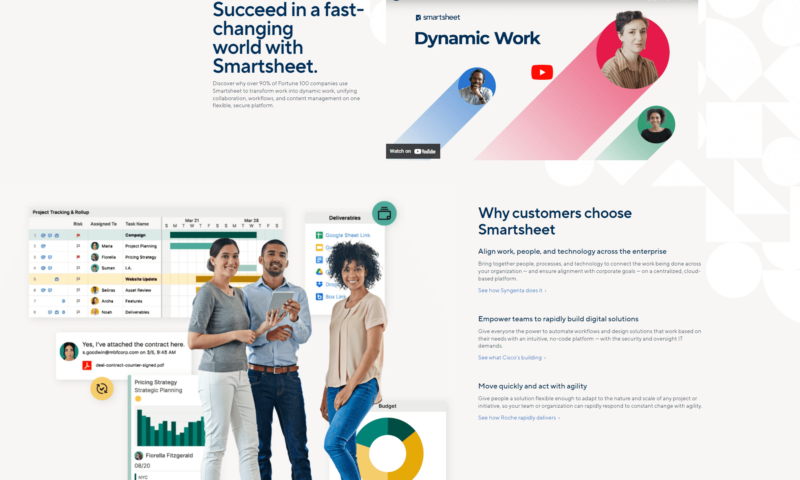
powerful spreadsheets that can help with calculation.
To do this, you divide the total overhead of each cost pool by the total of your cost drivers. This will give you a cost driver rate. You then multiply the cost driver rate by the number of cost drivers.
The math sounds complicated, but it’s easier than you think. The good news is software like Smartsheet (here’s our Smartsheet review) can help you do the calculations thanks to powerful spreadsheets. We’ll also show you an activity-based costing example below.
Activity-Based Costing: A Real Example
Let’s pretend that you manufacture keyboards. The first expense you encounter is molding the plastic keyboard shells, which has a cost pool total of $10,000. The cost driver for this process is the chemicals, which take 2,000 tubs. To get your cost driver rate, you divide the $10,000 cost pool by the 2,000 units, which equals $5 per mold ($10,000 / 2,000 = $5).
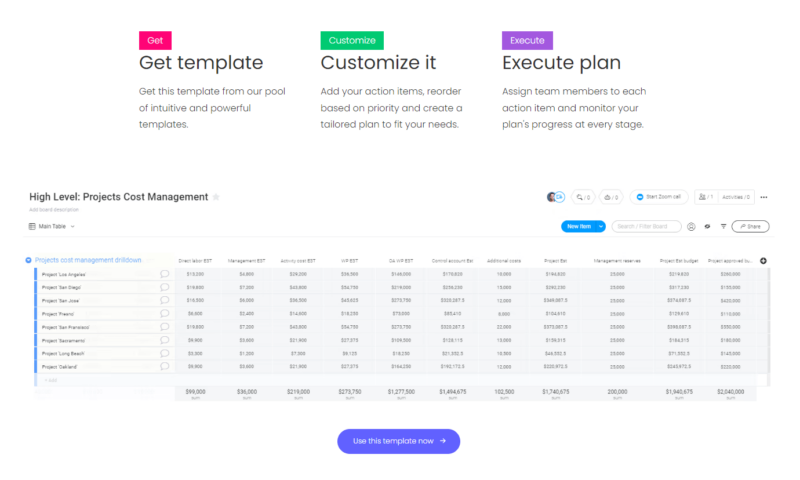
offer customizable templates that can help you generate budgets.
Now, suppose you want to scale up production. You simply multiply your cost driver rate by the number of cost drivers to get an estimated production cost. For example, if you want to create 10,000 keyboards, you know that you can do the simple math of 10,000 x $5 for a total run cost of $50,000.
You must run through this process for each cost pool and your cost drivers. Once you have done this, you will better understand the costs to manufacture your product, which will help you price your product correctly.
Advantages of Activity-Based Costing
With so many companies in the manufacturing space using activity-based costing methods, there are obviously some upsides to the method over traditional cost systems. Below, we’ll look at a few of the advantages of using this modern accounting system.
Better Budgeting
By using an activity-based costing system, you can paint a better picture of where company finances are going and what your total cost drivers are. Digging deep into each product you make by looking at the tools and resources used during production and their costs can help you better plan your finances.
Waste Elimination
An activity-based costing system, when used in conjunction with a Lean project management methodology such as kanban, can help companies cut down on wasteful processes that suck up time, resources and money.
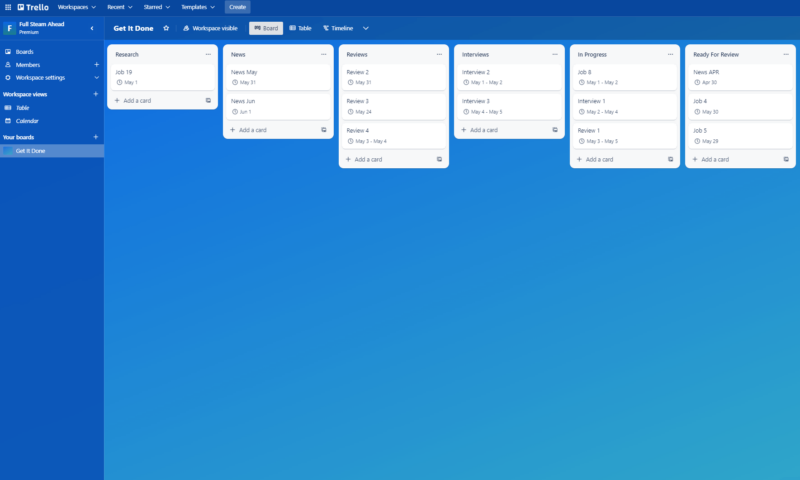
boards alongside an activity-based costing system.
Toyota used the Lean method during the 1940s to improve production and has since gone on to become the de facto standard for companies producing goods. If you need a solid kanban tool, check out our Trello review.
Increased Profit Margins
When used correctly, an ABC system should help increase profit margins. Through data collection, assigning costs to tasks and resources, and paying attention to where and how much money you’re spending, you can eliminate waste and better determine what price your products should be sold at to make a tidy profit.
Disadvantages of Activity-Based Costing
If a method has advantages, there are bound to be disadvantages. Unfortunately, activity-based costing is not immune here. Below, we’ll examine a few cons of implementing this cost accounting system.
Setting Up ABC Is Time-Consuming
Moving from a traditional system to an ABC system is a big undertaking that will require many hours of research, setting up software to track expenses and maintenance. It’s such a big undertaking that you need to hire a dedicated finance manager to keep up with everything. Fortunately, there are tools out there that can make switching to an ABC system easier.
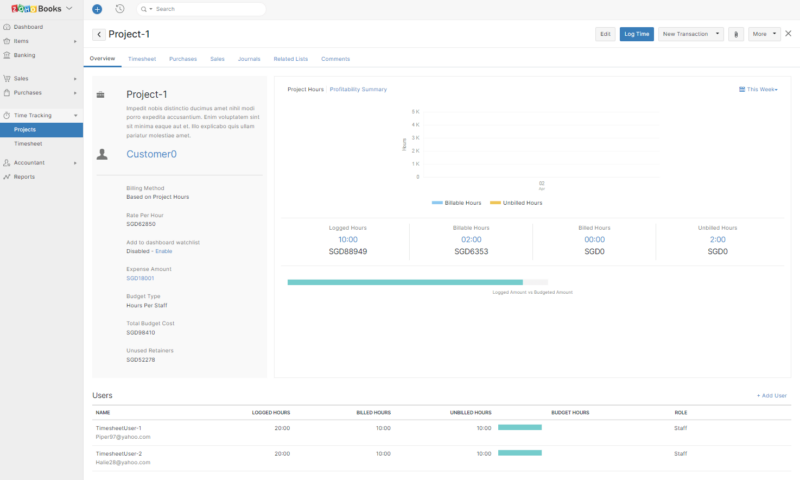
Software platforms such as ClickUp (here’s our ClickUp review) and monday.com (check out our monday.com review) can help you track expenses via tables (spreadsheets). Plus, dedicated accounting tools like Zoho Books (pictured above), which can integrate with Zoho Projects (here’s our Zoho Projects review), can help keep you on top of things.
Activity-Based Costing Systems Are Expensive
Compared to traditional costing methods, which account for generic overhead costs, activity-based methods are incredibly specific, which means you need to spend more time (and money) poring over data to analyze production costs accurately. Once in place, maintaining cost pools and micromanaging resources could eat into your bottom line.
Making Assumptions
While an ABC system is built on a foundation of research, it’s not going to be 100% accurate. You’re relying on data that your employees give you, such as how many hours a machine ran or how many hours an employee worked (humans aren’t always accurate).
There’s also cost data that may be outdated without you realizing it. While an ABC system is more accurate than traditional methods, don’t make assumptions about its accuracy. You’ll have to put in the work to maintain databases of information.
Final Thoughts
There are definitely advantages to running ABC systems over more traditional costing methods. Manufacturing companies that use activity-costing systems alongside lean management systems can see reduced waste, time saved and increased profits. Of course, implementing this system will take time and money to maintain, but the pros of ABC certainly outweigh the cons.
Have you switched to an ABC costing system? What do you like about it over the more simplified traditional methods? Would you recommend others in manufacturing industries make the switch? What software do you use to help you maintain your system? Let us know in the comments section, and as always, thanks for reading.
FAQ: The ABCs of Activity Based Costing
Activity-based costing is simply understanding what processes and resources your overhead costs are funding. By breaking down and analyzing company spending, you can better understand how to reduce waste, save money and price products.
Standard costing uses predetermined amounts for processes during manufacturing. In contrast, activity-based costing gets into the nitty gritty of the manufacturing process to determine accurate resource consumption levels and costs across multiple activities.
The four types of activity-based costing are unit-level, batch-level, product-level and facility-level.
The three objectives of activity-based costing are to provide accurate information for decision-making, to determine high-cost activities that can be cut down and to seek out non-essential processes.